What is 900D PU Coated Oxford Fabrics?

Explanation of its Composition and Characteristics
900D PU coated Oxford fabric is composed of a high-density polyester material that is coated with a layer of polyurethane (PU), resulting in a sturdy, durable fabric that can withstand harsh weather conditions and wear and tear. The PU coating on the fabric provides additional benefits, including water resistance and abrasion resistance, making it an ideal choice for outdoor gear and equipment. The fabric is also resistant to wrinkles and easy to care for, making it an excellent choice for travelers and adventurers who need gear that can withstand rugged environments. One of the key characteristics of 900D PU coated Oxford fabric is designed to withstand heavy use and resist tearing. Additionally, the fabric is available in a wide range of colors and finishes, making it easy for designers and manufacturers to create products that are both functional and aesthetically pleasing.
Comparison with Other Types of Oxford Fabrics

600D Oxford Fabric: 600D Oxford fabric is thinner than 900D Oxford fabric and is typically used for applications where a lighter-weight fabric is required. It is still durable and weather-resistant, but may not have the same level of strength and abrasion resistance as 900D PU coated Oxford fabric.
1680D Oxford Fabric: 1680D Oxford fabric is thicker and more durable than 900D PU coated Oxford fabric, making it an excellent choice for heavy-duty applications. However, it is also heavier and may not be suitable for applications where weight is a concern.
Ripstop Oxford Fabric: Ripstop Oxford fabric is a type of Oxford fabric that has a special reinforcing technique to make it resistant to tearing and ripping. It is often used in outdoor gear and equipment, but may not be as water-resistant as PU coated Oxford fabrics.
In comparison, 900D PU coated Oxford fabric is a good balance between weight, durability, and weather resistance. Its high-density polyester fibers and PU coating make it highly resistant to abrasion and water, while still being breathable and easy to work with.
Why Use 900D PU Coated Oxford Fabrics?
Advantages of 900D PU Coated Oxford Fabrics
Durability: Due to its high-density polyester fibers and PU coating, 900D PU coated Oxford fabric is exceptionally durable and resistant to tearing and abrasion.

Anti-UV: This feature is essential in applications where exposure to the sun is common, as it helps to protect the fabric from fading and degradation.

Versatility: 900D PU coated Oxford fabric is available in a wide range of colors and finishes, making it a versatile choice for designers and manufacturers.

Fire Resistance: 900D PU coated Oxford fabric can be treated with fire-resistant coatings to prevent it from catching fire and spreading flames.

Common Applications of 900D PU Coated Oxford Fabrics
Backpacks and Bags: 900D PU coated Oxford fabric’s strength and durability make it an excellent choice for backpacks, duffel bags, and other types of luggage.

Outdoor Gear: Tents, tarps, and other outdoor gear require fabrics that are waterproof, strong, and able to withstand harsh weather conditions. 900D PU coated Oxford fabric meets these requirements.

Automotive and Industrial: The high tensile strength of 900D PU coated Oxford fabric makes it ideal for use in the automotive and industrial industries, where it is used for covers, tarps, and other applications.

Medical Equipment: Some variants of 900D PU coated Oxford fabric have anti-bacterial properties, making them suitable for use in the medical industry.

Production Process of 900D PU Coated Oxford Fabrics
Explanation of the Manufacturing Process
Yarn Production: The first step is the production of polyester yarn. The yarn is produced by extruding molten polyester through spinnerets, which then solidify into continuous filaments.
Weaving: The polyester filaments are then woven into a fabric using a weaving machine. The weaving pattern determines the strength and durability of the final product.
Coating: Once the fabric is woven, it is coated with polyurethane (PU) to provide water resistance and durability. The PU coating is applied to the fabric using a coating machine, and the fabric is then dried and cured.
Inspection: The final step is an inspection to ensure that the fabric meets the required specifications: The fabric is inspected for defects, such as tears, snags, or holes, and it is also tested for water resistance and other performance characteristics.
In terms of specifications, 900D PU coated Oxford fabric typically has a weight of around 300-350 grams per square meter and a thickness of 0.55-0.6mm.
Factors to Consider when Selecting 900D PU Coated Oxford Fabrics
Durability and Strength
Since these fabrics are commonly used in heavy-duty applications, they need to withstand frequent wear and tear without losing their quality or integrity. A strong and durable fabric ensures that the product lasts longer and requires less maintenance or repairs. It’s also important to choose a fabric that meets the specific strength requirements of the application, whether it be for a backpack, luggage, or other product.
Water and Weather Resistance
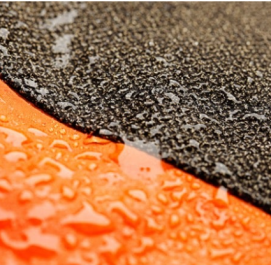
The PU coating on the fabric provides water resistance, which is essential for applications where exposure to moisture is a concern. Additionally, the fabric should be able to withstand exposure to different weather conditions, including rain, wind, and sunlight. Factors such as the fabric’s construction, weave, and thickness can affect its water and weather resistance.
Color and Appearance

The fabric is available in a variety of colors and finishes, including matte, shiny, and textured. The color and appearance of the fabric can affect its overall aesthetic appeal and can also impact its functionality in certain applications. For example, lighter colored fabrics may be more prone to staining or discoloration over time, while darker colors may absorb more heat in direct sunlight. Ultimately, the choice of color and appearance should be based on the intended use and the desired aesthetic of the final product.
How to Control the Quality of 900D PU Coated Oxford Fabrics in Production?
Control Measures on the Production Line

Raw Material Inspection: All raw materials, including the base fabric and the PU coating, should be inspected before use to ensure that they meet quality standards.
Process Control: Production processes should be carefully monitored and controlled to ensure consistency and accuracy in the application of the PU coating.
Testing and Inspection: Finished fabrics should be subjected to a series of tests and inspections, including tear resistance, tensile strength, water resistance, and abrasion resistance, to ensure that they meet the desired specifications.
Quality Assurance: A comprehensive quality assurance program should be in place, including regular audits and inspections, to ensure that quality standards are being met consistently throughout the production process.

Methods and Techniques for Inspection and Testing
Visual Inspection: A visual inspection is carried out to detect any defects such as discoloration, stains, or damage to the fabric’s surface.
Thickness Measurement: The thickness of the fabric is measured to ensure it meets the specified requirements.
Tensile Strength Testing: The tensile strength of the fabric is tested to ensure it meets the minimum strength requirements.
Tear Resistance Testing: The tear resistance of the fabric is tested to ensure it meets the specified standards.
Water Resistance Testing: The water resistance of the fabric is tested to ensure it can withstand exposure to water.
UV Resistance Testing: If the fabric is treated with anti-UV agents, UV resistance testing can be carried out to ensure its effectiveness.

Establishment of Quality Assurance and Control System
Use High-Quality Raw Materials: Quality control starts with the selection of high-quality raw materials, including fibers, dyes, and coatings.
Set Standards and Procedures: Establish clear standards and procedures for each stage of the production process, including weaving, dyeing, coating, and finishing.
Regular Inspections: Regular inspections should be carried out during production to ensure that the fabric meets the established standards and quality requirements.
Testing: Conduct tests on the fabric to check its physical and mechanical properties, including tensile strength, tear resistance, water resistance, and abrasion resistance.
Continuous Improvement: Continuously monitor the production process and make improvements where necessary to ensure consistent quality.
Conclusion
Firstly, the use of 900D PU coated Oxford fabric provides a reliable solution for bag manufacturers. Its high denier count ensures that the fabric can withstand heavy loads and frequent use, making it suitable for backpacks, duffel bags, and other luggage items. The strength of the fabric ensures that it can endure the rigors of travel and everyday use without easily tearing or showing signs of wear. This makes it an excellent choice for customers who prioritize durability and longevity in their products.
Secondly, the PU coating applied to the fabric enhances its water resistance. This is particularly beneficial for outdoor enthusiasts and campers who rely on tents made with 900D PU coated Oxford fabric. The coating acts as a protective barrier, preventing water from seeping through the fabric and keeping the interior dry even in wet conditions. This feature is crucial for ensuring comfort and protection during outdoor adventures, making the fabric an ideal choice for tent manufacturers.
Lastly, the Oxford weaving technique adds to the overall durability of the 900D PU coated Oxford fabric. This weaving technique creates a distinctive textured appearance, giving the fabric a unique aesthetic appeal. Furthermore, the crisscross pattern formed by the Oxford weave strengthens the fabric, making it less prone to fraying and improving its overall resistance to tearing. This makes the fabric a reliable choice for both bag manufacturers and fabric wholesalers who value quality and longevity in their products.
In summary, 900D PU coated Oxford fabric offers a combination of strength, water resistance, and durability, making it an excellent choice for bag manufacturers and fabric wholesalers. Its high denier count, PU coating, and Oxford weaving technique contribute to its exceptional performance and versatility. Whether it is used in the production of bags or tents, this fabric provides customers with reliable and long-lasting solutions, ensuring that their products withstand the test of time and various environmental conditions.