Product Overview
Definition and Composition of 1200D PU Coated Fabric
1200D PU coated fabric is a type of fabric that consists of a base material with a denier count of 1200 and is coated with polyurethane (PU) for added durability and water resistance. The denier count refers to the thickness or density of the individual fibers used in the fabric. In the case of 1200D fabric, it means that each filament in the base material has a thickness of 1200 deniers.
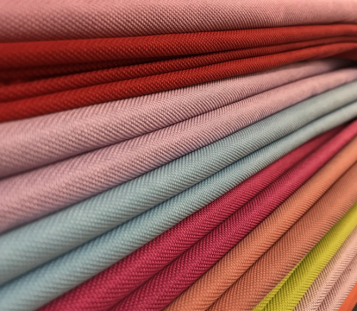
Significance of the 1200D Denier Count
The significance of the 1200D denier count lies in its strength and durability. Higher denier counts generally indicate a stronger and more resilient fabric. With a denier count of 1200, this fabric is considered to be quite strong, making it suitable for applications where sturdiness is required, such as bags, backpacks, and outdoor gear.

How does 1200D PU coated Fabric Compare to Other Materials like Nylon and Polyester?
When comparing 1200D PU coated fabric to other materials like nylon and polyester, there are a few key differences to consider. Nylon is known for its strength and abrasion resistance, making it a popular choice for heavy-duty applications. Polyester, on the other hand, offers excellent resistance to UV rays and is less prone to stretching and shrinking. Both nylon and polyester can be coated with PU to enhance their water resistance.
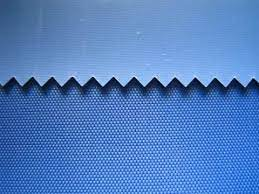
Compared to nylon, 1200D PU coated fabric may offer similar strength and durability. However, nylon fabrics are generally lighter in weight, which can be advantageous for certain applications. On the other hand, polyester fabrics coated with PU may provide better UV resistance and retain their color for a longer period.
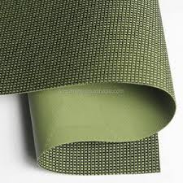
Importance of Understanding the Differences between Various coated Fabrics.
Understanding the differences between various coated fabrics is important for choosing the most suitable material for specific purposes. Different fabrics offer different properties and characteristics, such as strength, water resistance, breathability, UV resistance, and weight. By understanding these differences, one can select the appropriate fabric that meets the requirements of the intended application. For example, if water resistance is a priority, a fabric with a PU coating would be preferred, while if lightweight is important, a lighter nylon fabric might be a better choice.
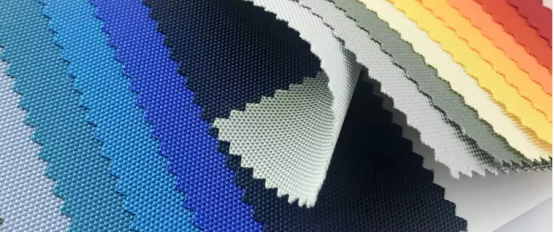
Key Features and Benefits
Durability: The 1200D denier count indicates a high level of strength and durability. This fabric is designed to withstand rigorous use and resist tearing or fraying, making it ideal for applications that require long-lasting performance.
Water Resistance: The PU coating on the fabric adds a layer of water resistance, making it highly resistant to water penetration. This feature helps protect the contents of bags or equipment made from this fabric from moisture damage, making it suitable for outdoor and travel gear.
Lightweight Nature: Despite its impressive strength, 1200D PU coated fabric maintains a relatively lightweight nature. This characteristic is particularly beneficial for applications where weight is a consideration, such as backpacks or lightweight equipment.
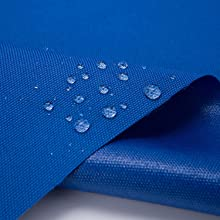
Applications of 1200D PU coated Fabric
The combination of durability, water resistance, and lightweight nature makes 1200D PU coated fabric highly versatile. It can be used in a wide range of applications, including but not limited to:
Bags and backpacks: The fabric’s durability and water resistance make it suitable for manufacturing durable and weather-resistant bags, backpacks, duffel bags, and luggage.
Outdoor gear: Tents, tarps, hammocks, and other outdoor equipment can benefit from the fabric’s ability to withstand rough outdoor conditions and repel water.
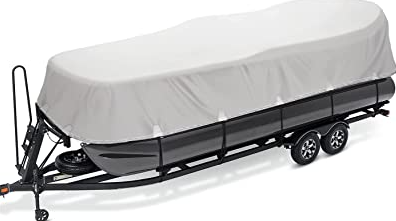
Covers and cases: The fabric can be used to create protective covers, cases, or sleeves for electronic devices, tools, or machinery due to its durability and resistance to moisture.
Sports and recreational equipment: Items like gym bags, sports gear bags, and equipment covers can benefit from the fabric’s durability and water-resistant properties.
Automotive and marine applications: The fabric can be used in automotive interiors, seat covers, and boat covers, where resistance to water and wear are important factors.
Industrial and heavy-duty applications: The fabric’s durability and strength make it suitable for industrial applications, such as protective covers, equipment cases, or heavy-duty bags.
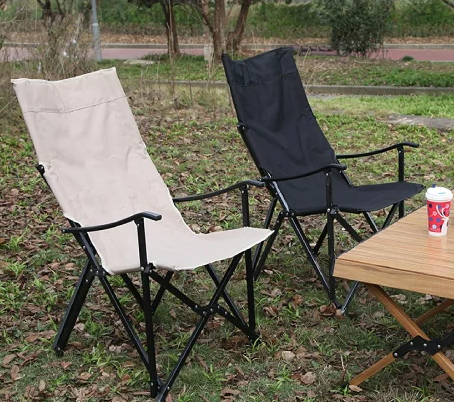
Factors to Consider When Importing 1200D Coated Fabric
Quality Standards and Certifications: Ensure that the fabric meets the required quality standards and certifications for your industry or specific application. Look for certifications such as ISO, ASTM, or relevant industry-specific certifications to ensure the fabric’s performance and durability.
Supplier Reputation and Reliability: Research and evaluate the reputation and reliability of potential suppliers. Consider factors such as their experience in the industry, customer reviews and feedback, and their ability to consistently deliver high-quality products on time.
Shipping and Logistics Considerations: Evaluate the logistics involved in importing the fabric, including shipping methods, transit times, customs regulations, and any associated costs. Consider the supplier’s ability to handle shipping and logistics effectively and their track record in delivering products without delays or damage.
Cost and Pricing Factors: Compare the costs and pricing structures offered by different suppliers. Consider the unit price of the fabric, any bulk order discounts, shipping costs, customs duties, and any other additional charges. Balance the cost with the quality and reliability of the supplier to ensure a cost-effective solution.
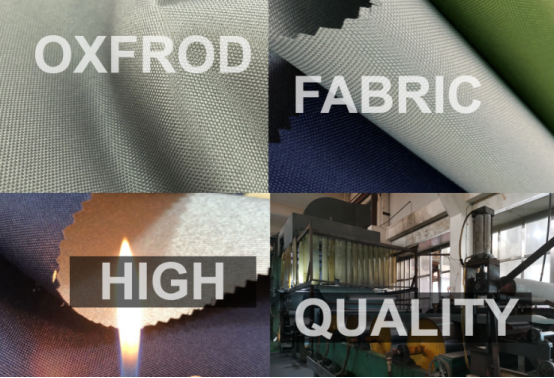
Factors Influencing Customer Selection: Understand the factors that influence your customers’ selection of coated fabric. This could include considerations such as color options, design flexibility, environmental sustainability, and other specific requirements. Choose a fabric that aligns with these customer preferences to increase your product’s appeal.
Quality, Cost-effectiveness, and Brand Image: Strive for a balance between quality and cost-effectiveness. The fabric should meet your quality requirements while also providing value for money. Additionally, consider how the fabric’s quality and cost affect your brand image. Using high-quality fabric can enhance your brand’s reputation, while overly high prices may deter customers.
Procurement Challenges
Sourcing Difficulties and Availability
One of the main challenges in procurement is finding reliable sources for the required materials or products. This may be due to limited suppliers in the market, geographic restrictions, or specific quality requirements. It can be challenging to identify and qualify suppliers who can consistently meet your needs in terms of quantity, quality, and delivery timelines. Additionally, fluctuations in demand, supply chain disruptions, and geopolitical factors can impact the availability of materials, making sourcing even more challenging.
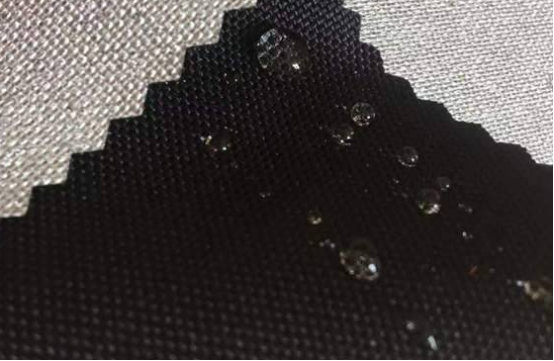
Pricing and Supplier Relationships
Pricing is a critical aspect of procurement, and it can be challenging to strike the right balance between cost and quality. Fluctuations in raw material prices, currency exchange rates, and market dynamics can impact pricing negotiations. It’s important to conduct thorough market research, benchmark prices, and assess the total cost of ownership to ensure you are getting the best value for your money. Balancing cost with quality and other factors such as reliability and support from suppliers is crucial in procurement decision-making.
Building and maintaining strong relationships with suppliers is vital for successful procurement. Challenges can arise when there is a lack of trust, poor communication, or misalignment of expectations between the buyer and the supplier. It’s important to establish clear communication channels, develop mutually beneficial partnerships, and manage expectations effectively. Developing long-term relationships with suppliers can help secure better pricing, timely deliveries, and access to additional support or resources.
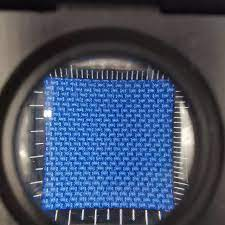
How to Choosing the Right Fabric
Considerations for Specific Application Requirements
Firstly, dentify your application requirements and understand the specific needs of your project or application. Consider factors such as the environment, intended use, and desired performance attributes.
Consider coating types, coatings provide different functionalities to the fabric. Common options include PVC, PU, acrylic, or silicone. Choose a coating type based on the desired properties such as water resistance, flame retardancy, UV resistance, or abrasion resistance.
Finishing Options and Customization
Explore customization options consider any specific customization requirements, such as custom colors, patterns, prints, embossing, or branding. Check if the fabric supplier offers customization options to meet your specific needs.
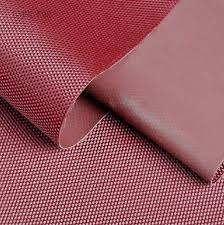
Quality Control of 1200D PU Oxford Fabric
Inspection and Testing Procedures
Visual Inspection: Conduct a visual inspection to identify any visible defects such as stains, discoloration, weaving irregularities, or coating inconsistencies.
Dimensional Inspection: Measure the fabric’s width, length, and thickness to ensure they meet the specified requirements.
Coating Thickness: Measure the coating thickness to verify it meets the required specifications.
Strength and Durability Testing: Perform tests to assess the fabric’s tensile strength, tear resistance, abrasion resistance, and bursting strength. This ensures it can withstand the intended use and environmental conditions.
Water Resistance Testing: Test the fabric’s water resistance by subjecting it to simulated rain or water pressure to determine its level of protection against moisture.
Flame Retardancy Testing: If flame retardancy is required, conduct tests to verify the fabric meets the relevant safety standards.
UV Resistance Testing: Assess the fabric’s ability to resist UV degradation by subjecting it to UV exposure and evaluating any color fading or material damage.
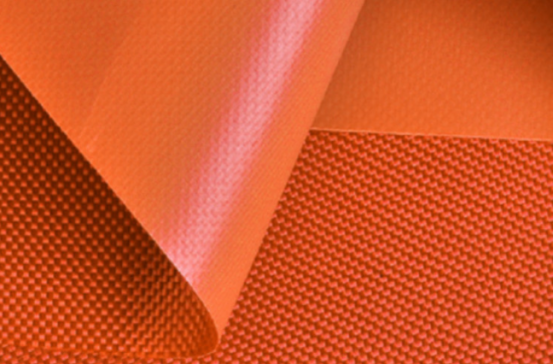
Standards for Defect Tolerance
Establish clear and measurable standards for defect tolerance based on industry standards, customer requirements, and the fabric’s intended use.
Define acceptable limits for defects such as weaving irregularities, coating imperfections, color variations, or other visual inconsistencies.
Classify defects based on severity, with different tolerance levels for major, minor, or cosmetic defects.
Document these standards and communicate them to fabric suppliers to ensure consistent quality across batches.
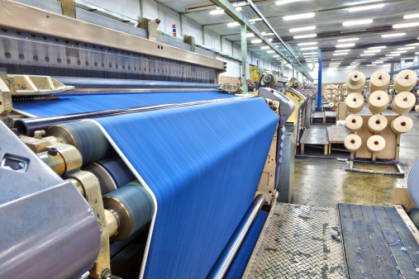
Criteria for Accepting or Rejecting Batches of Fabric
Define specific criteria for accepting or rejecting batches of fabric based on inspection and testing results.
Determine acceptable levels of defects, dimensional variations, coating thickness, and performance parameters.
If a batch fails to meet the predefined criteria, it should be rejected or subjected to rework and retesting until it meets the required quality standards.
Establish protocols for communicating quality issues to suppliers, ensuring prompt resolution and preventing non-conforming products from reaching customers.
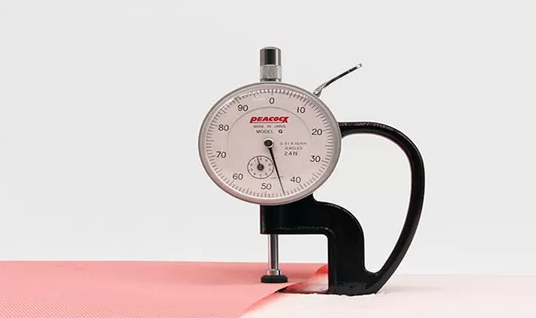
Importance of Quality Control
Ensuring Product Performance: Quality control measures help maintain consistent product performance by identifying and rectifying defects that could affect functionality or durability.
Customer Satisfaction: By delivering high-quality fabrics, manufacturers can meet customer expectations, enhance their reputation, and foster long-term relationships.
Compliance with Standards and Regulations: Quality control ensures compliance with industry standards, safety regulations, and customer-specific requirements.
Cost Reduction: Identifying and resolving quality issues early in the production process can minimize waste, rework, and customer returns, leading to cost savings.
Continuous Improvement: Quality control processes provide valuable feedback to improve production processes, enhance product design, and optimize material selection.
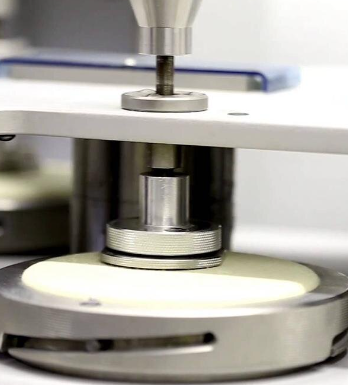
Conclusion
Emphasis on the Versatility and Performance of 1200D PU Coated Fabric
1200D PU coated fabric offers a versatile and high-performance solution for various applications. By considering specific requirements such as strength, durability, water resistance, flame retardancy, UV resistance, and abrasion resistance, you can select the right fabric for your needs. Customization options allow for personalization and branding.
Quality control measures, including inspection, testing, defect tolerance standards, and acceptance/rejection criteria, are essential to ensure consistent product performance and customer satisfaction. Adhering to industry standards and regulations is crucial for maintaining quality and meeting customer expectations.
Encouragement to Explore the Potential of this Textile
It is important to recognize the potential of 1200D PU coated fabric and explore its applications across industries. Its versatility, durability, and performance make it suitable for products such as bags, backpacks, tents, covers, and outdoor gear. By embracing this textile, you can unlock its benefits and create innovative and reliable products.
Investing in quality control and continuously improving production processes will contribute to the success of your products and strengthen customer trust. So, embrace the potential of 1200D PU coated fabric and utilize its versatility to meet the diverse needs of your customers.