Introduction
Introduce PVC Coated Fabric and Its Relevance
PVC coated fabric is a versatile material widely used in various industries due to its unique properties and applications. It consists of a base fabric that is coated with polyvinyl chloride (PVC) to enhance its performance and durability. PVC coated fabric finds applications in sectors such as automotive, construction, marine, and industrial, among others.
In these industries, PVC coated fabric is valued for its exceptional resistance to water, chemicals, UV radiation, and extreme weather conditions. It offers protection against abrasion, tear, and puncture, making it ideal for demanding environments. Additionally, PVC coated fabric provides flexibility, easy maintenance, and a wide range of design options.
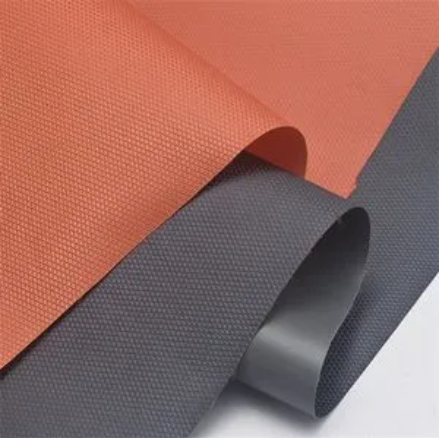
Wear Resistance of PVC Coated Fabric
The Definition and Impact of Wear Resistance
Wear resistance refers to the ability of PVC coated fabric to withstand friction, abrasion, and mechanical stress over an extended period without significant deterioration. It is a crucial characteristic as it directly affects the fabric’s durability and longevity.
When PVC coated fabric exhibits high wear resistance, it can endure harsh environmental conditions, repeated use, and contact with rough surfaces without experiencing excessive wear or damage. This ensures that the fabric remains intact, retains its functional properties, and continues to provide reliable protection or performance throughout its intended lifespan. By withstanding wear, PVC coated fabric can maintain its structural integrity, prevent tearing or puncturing, and avoid premature failure, resulting in cost savings and enhanced user satisfaction.

Economic Benefits of Using Wear-Resistant PVC Coated Fabric
Utilizing wear-resistant PVC coated fabric can bring several economic advantages to manufacturers, end-users, and industries as a whole.
Extended Product Lifespan: PVC coated fabric with high wear resistance lasts longer, reducing the need for frequent replacements. This translates into cost savings for manufacturers, as they can produce longer-lasting products with reduced maintenance and repair expenses. For end-users, it means lower replacement costs and increased value for their investment.
Enhanced Product Performance: Wear-resistant PVC coated fabric maintains its performance characteristics over time. Whether it is protecting goods from the elements, providing safety in hazardous environments, or ensuring structural integrity, the fabric’s consistent performance ensures optimal functionality and reliability, reducing downtime and enhancing overall efficiency.
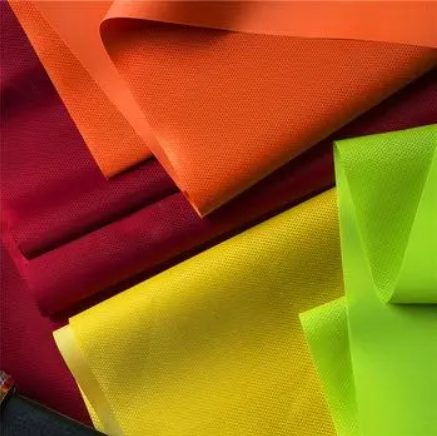
Reduced Maintenance and Replacement Costs: Wear-resistant PVC coated fabric requires less frequent maintenance, repair, or replacement, leading to reduced operational costs. Industries that rely on PVC coated fabric, such as transportation, construction, and agriculture, benefit from decreased downtime and lower expenditures on repairs or replacements, resulting in improved profitability.
Reputation and Customer Satisfaction: Utilizing high-quality, wear-resistant PVC coated fabric can enhance a company’s reputation for providing reliable and long-lasting products. Customers value durability and longevity, and when they experience products that meet or exceed their expectations, it leads to increased satisfaction, positive reviews, and potential repeat business or referrals.
Factors Affecting Wear Resistance PVC Coated Fabric
High-Quality Base Fabrics and Considerations for Abrasion Resistance
The selection of high-quality base fabrics is crucial in determining the wear resistance of PVC coated fabric. The base fabric serves as the foundation for the PVC coating and plays a significant role in determining the overall durability and wear resistance of the finished product. High-quality base fabrics with excellent tensile strength, tear resistance, and dimensional stability provide a solid starting point for achieving enhanced wear resistance.
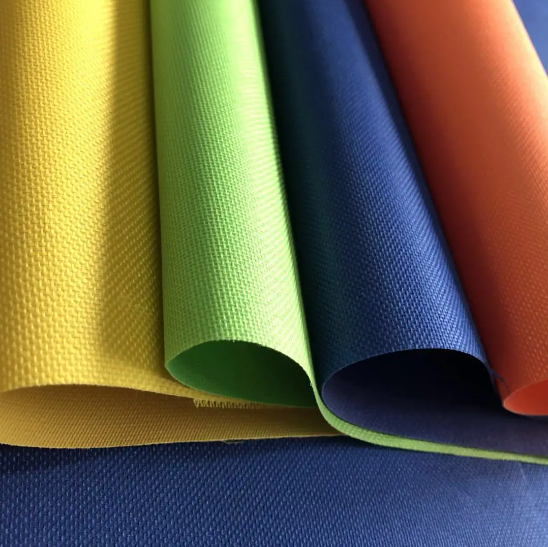
When selecting base fabric materials, several factors should be considered to ensure optimal wear resistance.
Strength and Durability: Choose base fabrics with high tensile strength and tear resistance to withstand external forces and abrasion.
Flexibility: Opt for fabrics that maintain flexibility and suppleness even after coating. This ensures the fabric can withstand repeated bending or flexing without cracking or losing its wear-resistant properties.
Dimensional Stability: Select fabrics with good dimensional stability to prevent excessive stretching, shrinking, or warping during use, which can compromise wear resistance.
Resistance to Environmental Factors: Consider the intended application and environmental conditions the fabric will be exposed to, such as UV exposure, moisture, chemicals, or extreme temperatures. Choose base fabrics that demonstrate resistance to these factors to maintain wear resistance over time.
Influence of Coating Methods on Wear Resistance
The coating method employed during the manufacturing process significantly impacts the wear resistance of PVC coated fabric. Different coating techniques, such as knife coating, roller coating, or dip coating, have varying effects on wear resistance. Factors such as coating thickness, uniformity, and adhesion to the base fabric play a crucial role in determining the fabric’s resistance to wear and abrasion.
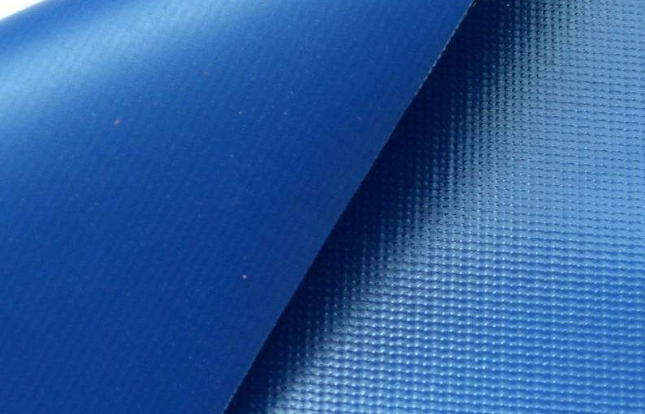
Introduction to Advanced Coating Technologies that Improve Wear Resistance
Advancements in coating technologies have allowed for the development of PVC coated fabrics with superior wear resistance. Some notable technologies include:
Multi-layer Coatings: Applying multiple layers of PVC coating with varying properties can enhance wear resistance. This approach allows for the combination of different formulations, each providing specific benefits, such as improved abrasion resistance or flexibility.
Cross-linking Agents: Introducing cross-linking agents during the coating process can enhance the strength and durability of the PVC coating, resulting in improved wear resistance.
Nano-Coatings: Nanostructured coatings utilize nanoparticles to create a protective layer that enhances wear resistance. These coatings provide additional barriers against abrasion, UV degradation, and chemical exposure, thereby extending the fabric’s lifespan.
Role of Additives in Enhancing Wear Resistance Properties
Additives are substances incorporated into the PVC coating to enhance specific properties, including wear resistance. Some common additives used to improve wear resistance in PVC coated fabric include plasticizers, stabilizers, flame retardants, and anti-microbial agents. These additives can modify the physical and chemical characteristics of the coating, making it more resilient to wear and environmental stressors.
Several additives and enhancements contribute to improved wear resistance in PVC coated fabric.
Reinforcing Fillers: Incorporating reinforcing fillers, such as carbon black or silica, can enhance wear resistance by increasing the fabric’s strength and resistance to abrasion.
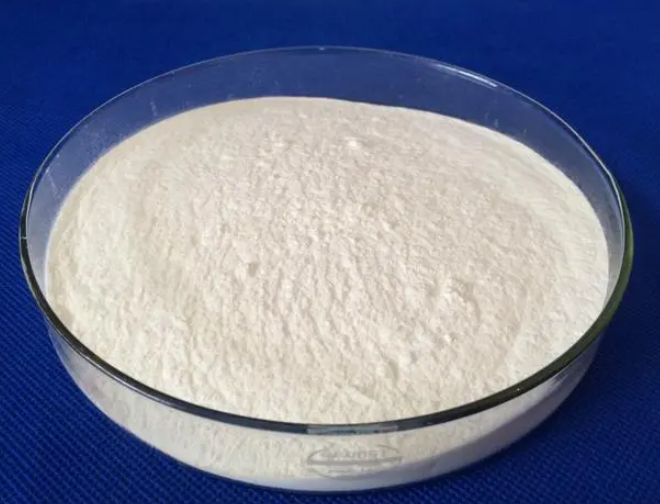
UV Stabilizers: UV stabilizers protect PVC coated fabric from UV degradation, preventing premature wear caused by prolonged exposure to sunlight.
Anti-friction Coatings: Applying anti-friction coatings or finishes to the PVC coated fabric’s surface can reduce friction, thereby minimizing wear and extending the fabric’s lifespan.
Anti-static Agents: Adding anti-static agents to the PVC coating can reduce the accumulation of static electricity, which can attract dust and particles that accelerate wear.
By carefully selecting additives and incorporating suitable enhancements, PVC coated fabric manufacturers can significantly enhance wear resistance and ensure the fabric meets the specific demands of various applications.
These factors—material selection, coating technology, and additives/enhancements—play vital roles in determining the wear resistance of PVC coated fabric. Manufacturers must consider each aspect carefully to produce high-quality, wear-resistant fabrics that meet the performance requirements of their customers.
How to Purchase Wear-Resistant PVC Coated Fabric
Learn about the Issues Customers Face with Wear Resistance
To address customer pain points related to wear resistance, it is essential to have a clear understanding of their specific requirements. Engage with customers to gather information about the intended application, environmental conditions, and performance expectations. By understanding the unique demands placed on the PVC coated fabric, you can better address their wear resistance concerns.
Listen to your customers to identify the challenges they face when it comes to wear resistance in PVC coated fabric. Some common pain points may include premature fabric failure, reduced product lifespan, or increased maintenance costs due to inadequate wear resistance. By acknowledging these challenges, you can tailor your solutions to address their specific pain points effectively.
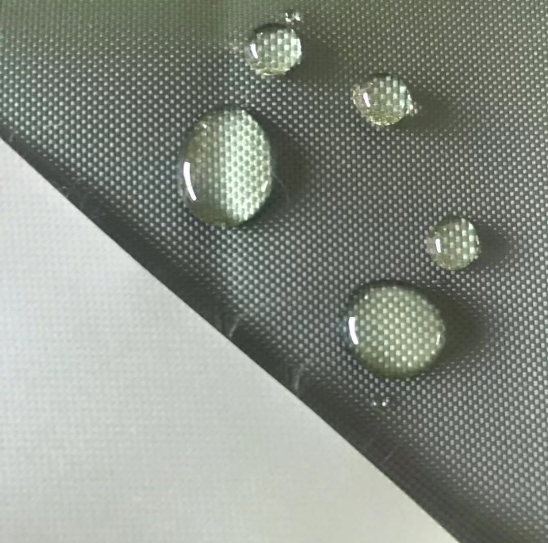
Provide Tailor-made Solutions to Solve Customer Needs
Providing customized solutions is crucial in addressing customer pain points related to wear resistance. By offering a range of options, such as different base fabric materials, coatings, and additives, you can tailor the PVC coated fabric to meet the specific needs of each customer. Collaborate closely with customers to understand their unique requirements and develop custom solutions that optimize wear resistance while considering other factors like budget and performance.
How to Choose the Right Wear Resistance
Research Industry Standards and Regulations
Familiarize yourself with industry standards and regulations that relate to wear resistance in PVC coated fabric. These standards often provide guidelines and benchmarks for assessing wear resistance performance. Understanding these standards helps you set appropriate performance targets for the fabric.
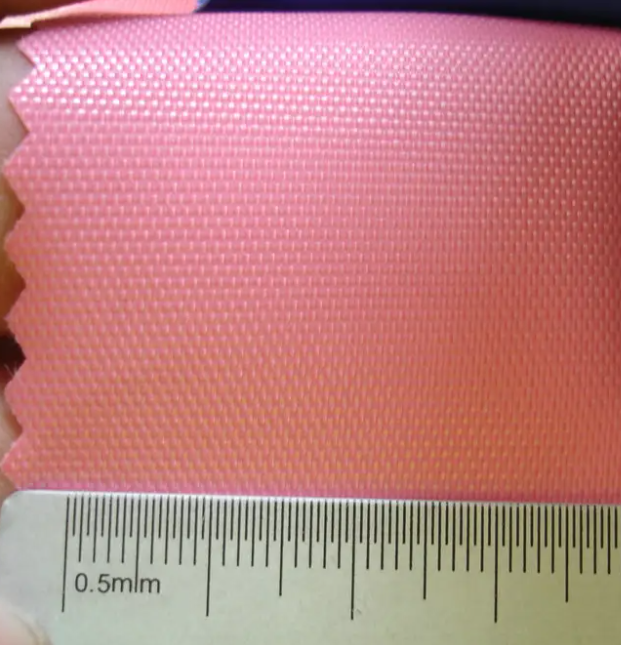
Consideration of Expected Service Life and Performance Expectations
Determine the expected service life of the PVC coated fabric and the desired performance characteristics. Consider factors such as the frequency and intensity of use, the expected lifespan of the end product, and any specific performance requirements. These considerations will help you establish the level of wear resistance necessary to meet the performance expectations.
Observation of Product Specifications and Technical Data
Thoroughly examine the product specifications and technical data provided by the PVC coated fabric manufacturer. Look for information related to wear resistance, such as test results, material composition, coating thickness, and any additives or enhancements that contribute to wear resistance. Analyze this data to assess if the fabric aligns with the desired wear resistance level.
Field test of Samples
Request samples of PVC coated fabric that meet your initial criteria for wear resistance. Conduct field trials to evaluate the fabric’s performance under real-world conditions. Assess its durability, resistance to abrasion, and overall wear characteristics. This hands-on evaluation allows you to make informed decisions based on the fabric’s actual performance.
Feedback from Existing Users
Reach out to existing users of PVC coated fabric with similar wear resistance requirements. Request their feedback and experiences with different products. Their insights can provide valuable information on the fabric’s performance in specific applications and help guide your decision-making process.
Quality Control Measures for Ensuring Wear Resistance
Implement Rigorous Quality Checks on Base Fabric Materials
To ensure wear resistance in PVC coated fabric, it is crucial to conduct thorough inspections of the base fabric materials. Implement stringent quality control measures to assess the quality, strength, and durability of the raw materials. This includes checking for defects, verifying tensile strength, tear resistance, and dimensional stability. By ensuring the use of high-quality base fabrics, the foundation for wear resistance is established.
During the raw material selection process, prioritize materials that possess suitable wear resistance properties. Consider factors such as the type of fiber, weave construction, and surface characteristics. Choose materials that have a proven track record of excellent wear resistance and can withstand the specific demands of the intended application.
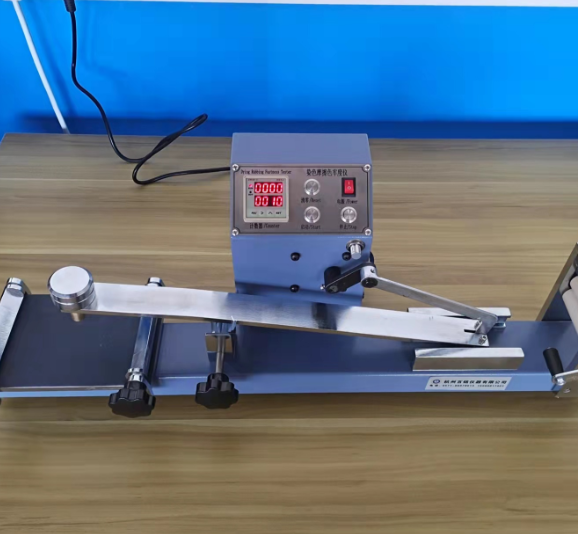
Strict control Measures in the Coating to Enhance Wear Resistance
Implement rigorous control measures throughout the coating process to optimize wear resistance. This includes closely monitoring coating parameters such as coating thickness, uniformity, and adhesion to the base fabric. Establish standardized operating procedures and quality checks to ensure consistent and reliable coating application. By maintaining tight control over the coating process, you can enhance the fabric’s wear resistance and overall quality.
Continual monitoring and improvement of coating techniques are essential for maintaining consistent quality and improving wear resistance. Regularly evaluate and analyze coating processes to identify areas for optimization. This may involve refining coating equipment, adjusting process parameters, or exploring innovative coating technologies. By staying proactive in process improvement, you can enhance wear resistance and ensure the consistent delivery of high-quality PVC coated fabric.
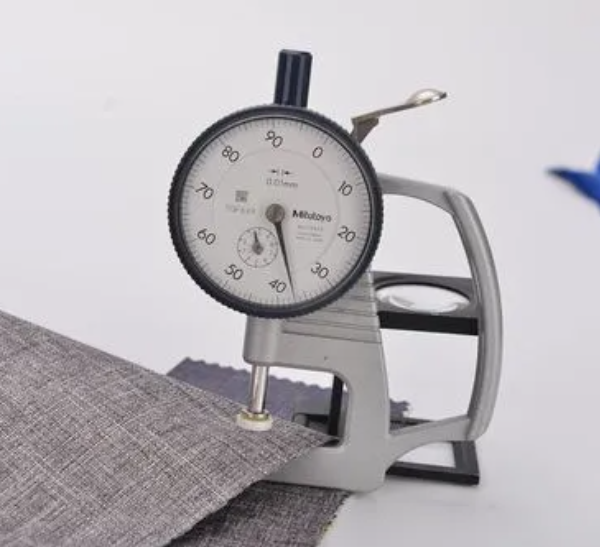
The Importance of Quality Testing for Fabric Wear Resistance
Testing is a critical quality control measure for assessing wear resistance in PVC coated fabric. Utilize standardized testing methods, such as abrasion resistance testing (e.g., Martindale or Taber abrasion) and flex testing, to evaluate the fabric’s performance under wear conditions. These tests simulate real-life wear and measure the fabric’s ability to withstand friction and mechanical stress. By conducting comprehensive wear resistance testing, you can validate the fabric’s durability and ensure it meets the desired wear resistance standards.
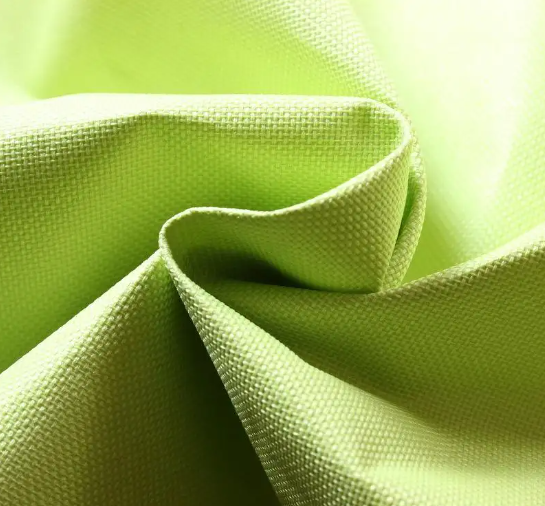
Highlight the significance of testing as a quality control measure to ensure wear resistance. Emphasize that testing is not only a validation of product performance but also a means to identify potential issues or areas for improvement. By integrating testing as an integral part of the quality control process, you can identify and rectify any deviations from desired wear resistance specifications, ensuring the consistent delivery of high-quality PVC coated fabric to customers.
Conclusion
This comprehensive article explores the importance of wear resistance in PVC coated fabric and provides a detailed understanding of various aspects related to wear resistance. It highlights how wear resistance directly affects the longevity, reliability, and performance of PVC coated fabric, making it crucial for demanding applications. The article discusses the economic benefits of using wear-resistant fabric, factors influencing wear resistance such as material selection, coating technology, and additives/enhancements. It also provides guidance on purchasing wear-resistant PVC coated fabric, including identifying customer needs, customization, and consultation. Additionally, the article offers insights into assessing application needs, evaluating performance standards, and quality control measures. Overall, the article aims to educate readers on wear resistance in PVC coated fabric and empower them to make informed decisions when selecting and utilizing this type of fabric.