Introduction
Before we dive into customization, let’s get acquainted with our star player: the 600D Oxford fabric. This material, known for its durability and versatility, is commonly used in various outdoor applications. Its key features include:
Strength: 600D Oxford fabric is tough and resilient, making it ideal for products that need to withstand wear and tear.
Water Resistance: The material’s PU or PVC coating provides excellent water resistance, ensuring your products stay dry even in adverse conditions.
Versatility: It’s used in an array of products such as bags, backpacks, luggage, tents, and raincoats, making it a top choice for outdoor enthusiasts.
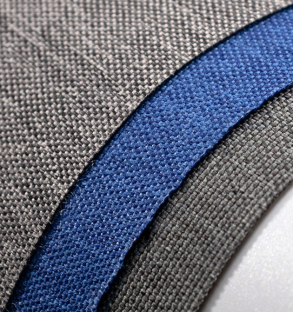
Customization Options
Printing Options
Sublimation Printing: This method allows for high-resolution, full-color printing. Sublimation ink transforms into a gas when heated, penetrating the fabric’s fibers for long-lasting and vibrant prints.
Screen Printing: Ideal for bold, solid colors and sharp designs. Screen printing provides excellent color saturation and durability.
Digital Printing: Perfect for intricate designs and photorealistic images. It offers flexibility in print size and design variations.

Embroidery and Labeling
Another popular customization option involves embroidery and labeling:
Classic Elegance: Embroidery adds a touch of classic elegance, offering tactile and premium finishes for logos, brand names, or custom artwork.
Durability: Embroidery stands up to rugged use and multiple washes, making it an excellent choice for items subjected to wear and tear.
Logo Patches and Labels: Custom logo patches or labels can give your products a distinct identity, whether sewn on or heat-sealed for a sleek finish.

Additional Customization Elements
Beyond printing and embroidery, there are other customization elements to consider:
Heat Transfer Printing: Ensures precise placement of graphics, ideal for branding and logos.
Custom Dyeing: For unique color requirements, custom dyeing can match your brand’s specific color palette.
Reflective Elements: Enhance safety with strategically placed reflective elements for better visibility in low-light conditions.
Zipper Pulls and Accessories: Elevate both the aesthetics and functionality of your products with customized zipper pulls and accessories.
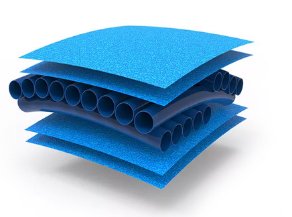
Customization Process
Design Consultation and Approval
Consultation and Design Discussion: We initiate the customization process with a thorough consultation to understand your vision, design specifications, and preferences.
Design Approval: After gathering your requirements, our skilled designers create a digital mock-up of your design for your review and approval. This step ensures your vision is accurately captured before production begins.

Production and Quality Assurance
Production and Printing/Embroidery: Once your design is approved, our production team employs advanced equipment and craftsmanship for printing or embroidery, ensuring precise and vibrant results.
Quality Assurance: Quality control is paramount. Each customized item undergoes rigorous inspections to meet both your specifications and our quality standards. Any deviations or imperfections are promptly addressed and corrected.

Final Review, Packaging, and Delivery
Final Review and Approval: Before shipment, we provide a final sample of your customized product for your review and approval, ensuring it aligns perfectly with your expectations.
Packaging and Delivery: Your approved customized products are carefully packaged to guarantee they arrive in excellent condition. Our efficient shipping process ensures prompt delivery according to the agreed-upon timeline.

Manufacturing Process
Material Procurement and Customization
We begin by sourcing premium 600D Oxford fabric with PU or PVC coating from trusted suppliers.
Your customization journey starts with our skilled designers, who work closely with you to create digital designs that align with your vision.
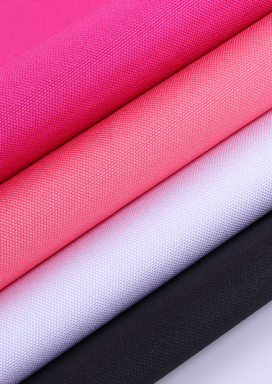
Printing, Assembly, and Quality Control
Advanced printing techniques or skilled embroidery are employed to bring your designs to life on the fabric.
Fabric components are precision-cut and meticulously assembled, with strict attention to detail.
Rigorous quality control checks are conducted at every stage to ensure color accuracy, stitching quality, and overall craftsmanship.

Final Product Assembly, Packaging, and Shipping
After quality checks, we assemble the final product, attaching any necessary features or hardware.
Each item undergoes a final inspection to ensure it meets design specifications.
Secure and eco-friendly packaging methods are employed to protect your products during transit.
Timely delivery is a priority, and we partner with trusted shipping providers to ensure on-time delivery, including international shipping options.

Shipping Process
Packaging and Shipping Method Selection
Packaging: We prioritize the safety of your customized products during transit. Our skilled packaging team individually inspects each item and uses high-quality materials to ensure they are well-protected.
Shipping Method Selection: We offer a range of shipping methods tailored to your needs. Whether you require expedited shipping or a cost-effective solution for bulk orders, our logistics team will guide you in choosing the best option.
Documentation: Our experienced logistics team takes care of all necessary documentation, including customs clearance and export paperwork, to ensure a smooth transit process.
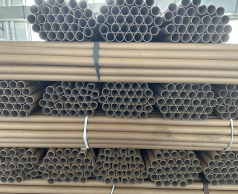
Tracking, Delivery, and Customer Support
Tracking and Updates: We provide tracking information so you can monitor your shipment’s progress in real-time. Our customer support team is also available to address any questions or concerns during transit.
Delivery: We work with trusted shipping partners to ensure your products arrive safely and within the agreed-upon timeframe, regardless of the order size.
Quality Assurance Upon Arrival: Upon receiving your order, we recommend inspecting the products to ensure they have maintained their quality during shipping. We stand by the quality of our products and are here to address any concerns.
Customer Support: Our commitment to you extends beyond delivery. Our customer support team is ready to assist you with any questions, concerns, or feedback, ensuring your satisfaction throughout the entire process.

Quality Control Process
Material and Production Inspection
Material Inspection: We start by meticulously inspecting the raw 600D Oxford fabric to ensure it meets specifications in terms of weave, coating uniformity, color accuracy, and defect detection.
Production Line Monitoring: Our quality control team closely oversees the entire production process, from cutting to assembly, ensuring compliance with established standards.

Customization and Structural Checks
Printing and Embroidery Inspection: For customized orders, we perform thorough checks to verify design accuracy and alignment, ensuring they match our clients’ specifications.
Dimensional and Structural Checks: We assess each product’s measurements and structural integrity to ensure proper fit and functionality.
Stitching and Seam Inspection: Close attention is paid to the strength, spacing, and alignment of stitches and seams to prevent weak points.

Durability and Final Inspection
Durability Testing: To ensure products can withstand outdoor use, we subject samples to rigorous tests, including abrasion resistance, tear strength, and water repellency evaluations.
Color Fastness Testing: The color vibrancy and longevity of printed or embroidered designs are evaluated for resistance to fading when exposed to environmental factors.
Final Inspection: Before leaving our facility, products undergo a comprehensive final inspection that reviews all quality checks conducted throughout production. Only items meeting our stringent standards are cleared for packaging and shipping.
Documentation and Traceability: We maintain thorough documentation of all quality control processes, providing transparency and the ability to trace the production history of each item, ensuring the highest level of assurance for our clients.

Conclusion
In the world of outdoor product manufacturing, the choice of fabric can make all the difference. 600D Oxford fabric, with its impressive strength, durability, and versatility, has become a staple for creating products that can withstand the rigors of the great outdoors. What sets it apart is not just its ruggedness but also its adaptability for customization through printing and embroidery.
Our Commitment to Quality: We take pride in our commitment to quality. Our production process is a carefully choreographed symphony of precision, from material procurement to final inspection. When you choose to customize with us, you’re not just getting a product; you’re getting a masterpiece crafted with dedication and attention to detail.
Seamless Collaboration: Our customization process is a partnership with our clients. We listen to your needs, understand your vision, and work tirelessly to turn your ideas into reality. Our communication is transparent, and our production scheduling ensures that your customized products are delivered on time, every time.
In conclusion, when you choose 600D Oxford fabric for your outdoor product needs, you’re choosing more than just a material; you’re choosing a world of possibilities.